Whether you’re a fleet manager, a truck driver or a mechanic, you’re probably aware of the problems jackknifing can cause. When parking in small spaces or navigating around narrow curves, the trailer can sometimes end up in a very tight angle against the truck.
Professional drivers can deal with these situations and position the trailer at the tightest possible angle without causing any damage. But accidents can happen, and when the angle becomes too tight, the vehicle has jackknifed.
Luckily, there’s a simple solution that can drastically cut the risk of a jackknife ever happening. I’ll explain how it works in this article.
Risk situations for jackknifing
Jackknifing is one of the most common accidents that can occur with a truck and trailer.
Most jackknifing incidents happen at low speeds during reversing, especially during tricky manoeuvres on very narrow, curved roads, like logging roads or at construction sites. This kind of incident causes serious problems with downtime, elevated maintenance costs, missed deliveries and difficult logistics planning. Stress and poor visibility can result in even a highly skilled senior driver ending up in a jackknifing situation.
It’s not possible to say the exact angle at which a jackknife will occur – the vital angle always depends on the construction and dimensions of the truck and trailer. This is one of the many reasons why experienced truck drivers are such a valuable resource in a truck fleet!
The damage and cost that jackknifing can cause
When a jackknife happens, the combined forces of the truck and trailer folding in against each other place huge strain on the equipment, particularly the coupling. The drawbar pulls powerfully against the locking bolt and pushes against the body of the coupling, bending or cracking the coupling and bolt and the rest of the mounting assembly, like the drawbeam, drawbar or mounting plates. It can also cut off the electrical and pneumatic connections between the truck and the trailer.
Maintenance is needed to fix the damage, and in many cases an expensive complete replacement of the assembly is required.
But that’s just the repair bill. A fleet manager will see even more costs due to lost productivity, missed deliveries, customer dissatisfaction and other planning issues caused by sudden downtime.
How to prevent jackknifing damage
The best way to minimise the risk of jackknifing incidents in a truck fleet is to have experienced, well-trained drivers. Drivers who know their vehicles and can manoeuvre them expertly are unlikely to cause serious damage by jackknifing.
However, accidents can happen, and even the most skilled driver can make a mistake. For that reason, an active warning system is a fantastic add-on.
Our jackknifing warning system consists of a sensor device mounted on the coupling itself. The maximum safe turning angle is specified at installation, and when the angle between the truck and trailer becomes dangerously tight, the driver is warned with an audio signal in the cabin.
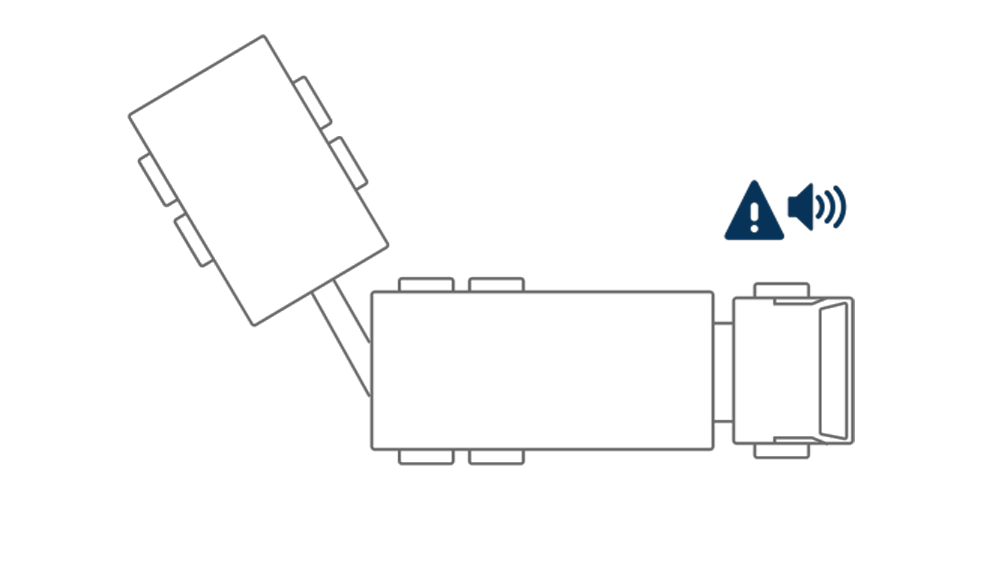
The jackknife indicator recognises the critical angle and warns the driver before a jackknife occurs.
Installing warning systems like these in a fleet requires an initial investment – but fleet managers can quickly see a return when expensive jackknifing incidents are avoided.
Take a look at our jackknife indicator system for more details – and get in touch if you want to learn more about how it could be implemented in your fleet.
