Truck industry trends to be aware of in 2024
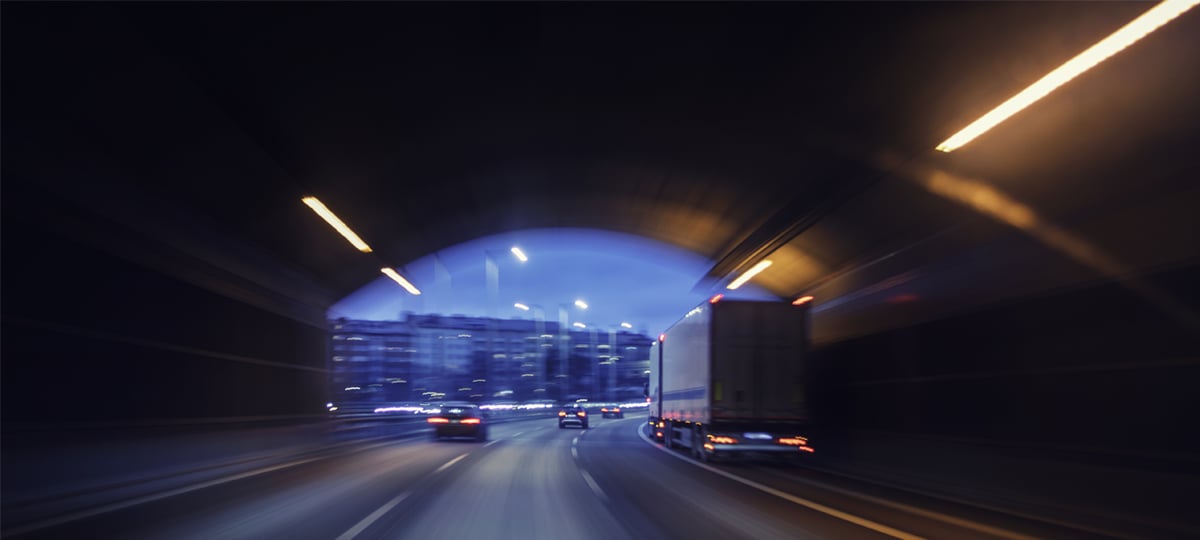
The interconnected world has made smooth, reliable logistics more important than ever. As the demand for sustainability and efficiency grows, our industry faces many challenges and opportunities that will characterise 2024 and the rest of the decade.
Some of these developing trends, such as sustainability and electrification, will have a long-term impact on the truck business and open up new avenues of exploration. Others, like supply chain disruptions, will likely make life more complex in logistics, particularly for body builders.
Whether the changes are positive or negative, preparing for the future is essential. In this article, I'll detail some of the main trends I believe will affect our industry this year and beyond, using insights from industry organisations and commentators.
- Sustainability and electrification
- Circularity and the growth of the circular economy
- A changing supply chain situation
- New driver aid technologies and autonomous driving
Hopefully, you will find some insights into the direction your business will move in the near future.
Sustainability and electrification
You don't have to be part of the truck industry to have noticed sustainability rising up the agenda over the last few years. Now, most large companies have some sort of sustainability policy in place, and others are setting ambitious sustainability goals for the future. At the same time, governments and regulators are putting pressure on businesses to become more sustainable – look at the EU's proposed 2035 ban on new petrol and diesel-driven cars and vans and the emissions regulations on heavy goods vehicles that are likely to follow. Actors in our industry will have to change rapidly by boosting their supply chain sustainability and electrifying their fleets, or implementing other zero-emission technologies like fuel cells. Progress is already being made – both established truck manufacturers and newcomers have already released electric or hydrogen-powered fuel cell trucks, and in September 2023, Swedish manufacturer Scania even opened its own battery assembly factory to meet its electric ambitions.
A change as large as this naturally creates some practical challenges. In the 2022 annual report from the VDA, the German automotive industry association, the scale of the infrastructure needed to support electrified road traffic is made very clear:
- By 2030, more than one million charging points will be needed in Germany to support the projected number of electric cars, vans and trucks that will be on the roads. 2,000 charging points must be installed a week to achieve this goal – far more than the 300 to 350 that are installed weekly today. The pace needs to increase, both in Germany and across Europe, to keep trucks rolling in the future.
- Charging points must be strategically placed across major transport routes, such as motorways, to support long-distance transports.
- Companies that produce trucks and trailers, as well as bodybuilders, will need to make significant changes to their production processes and even retrain their workforce to build their expertise in electric technology.
Clearly, moving towards fully-electrified trucking isn’t just a job for the truck industry. ACEA, the European Automobile Manufacturers’ Association, made this clear in October 2023 when they warned that European emissions targets will be impossible to reach without investment in infrastructure and customer demand. As ACEA Director General Sigrid de Vries said, “ACEA’s members have made the investments, and zero-emission vehicles are ready to go, but customers must equally have the confidence to invest.”
Sustainability will go from being a buzzword to a vital part of business during this decade – but progress in the truck industry may be held back by infrastructural delays and growing pains.
Circularity and the growth of the circular economy
Circularity is another major trend within sustainability that has exciting applications in the truck industry. In a circular economy, products are reused at the end of their life, rather than being scrapped and replaced with newly-manufactured products. Through processes like recycling, refurbishment, reuse or remanufacturing, the materials used in a product can get a second life rather than being discarded.
As progress is made in electrification and other zero-emission drivetrain technologies, the emissions generated during a truck’s working life will be reduced significantly. So, in order to continue making their businesses more sustainable, manufacturers will have to start making improvements upstream and downstream – in the truck manufacturing process and at the end of a truck’s useful working life. This is where circularity comes in.
All industries have the opportunity to become more circular, and the infrastructure and processes needed to make the economy truly circular are likely to mature significantly over the next decade.
In the truck industry, circularity creates new opportunities for body builders – look at the example of Danish logistics company DSV, which during 2023 aimed to double the service life of 1,100 trailers by taking a circular approach. Typically, the company's trailers are returned to the leasing company or manufacturer at the end of their five-year service life and replaced with new ones. Instead, the trailers were refurbished and returned to their original standard to stay in service for another five years. According to Dutch leasing company TIP, which was involved in the project, manufacturing a new trailer generates 18.6 tons of carbon, compared to only 2.7 tons for refurbishment.
Initiatives like this are likely to become more common as the pressure grows for companies to boost sustainability across a product’s entire lifecycle – not just when it’s being used.
A changing supply chain situation
Global supply chain issues have affected all kinds of business in recent years, and the truck industry is no exception. Truck manufacturers, bodybuilders and fleet managers have suffered from manufacturing challenges as essential materials become more expensive and harder to source. Long and unpredictable lead times made long-term planning difficult and created serious inefficiencies.
For some companies in certain markets, the outlook is still negative. In an August 2023 survey of 46 German companies conducted by the German Confederation of Skilled Crafts (ZDH), over a quarter claimed they were currently facing economic difficulties. Of those companies, over half blamed a rise in procurement prices that made fulfilling orders uneconomical, while almost a third said delivery bottlenecks had caused them to postpone or cancel customer orders.
However, other figures suggest that a recovery is occurring. Statistics from ACEA showed that the number of new truck registrations had increased by 20% in the first half of 2023 compared to the same period in 2022. New registrations for other types of commercial vehicles also increased, a trend that ACEA attributed to an improving supply chain situation.
Although the worst days of the supply chain crisis seem to be over, it looks like business in our industry working with production and construction will continue to face uncertainty in 2024 and beyond.
New driver aid technologies and autonomous driving
This trend is a little more distant than the others – the industry won't be directly struggling with the challenges of self-driving trucks this year as they are with supply chain and charging infrastructure issues. However, it's an important development that will affect the way of working for every company that works with trucks – from logistics firms and truck manufacturers to body builders and drivers.
Self-driving technology has been a fact of life in the car industry for a long time, although fully autonomous driving still looks a long way off. Progress has been slower in the commercial vehicle and logistics industry due to technical challenges, but expect research and development to ramp up soon. The VDA, along with its research arm FAT, is currently working on a project that aims to iron out some of the lingering issues that are holding advanced driver aids back:
- Perfecting the truck-trailer interface – to assist the driver and boost operational efficiency as much as possible, large amounts of electronic data need to be transmitted between the truck and the trailer, from information about position, forces and temperature to video feeds from onboard cameras. Existing standard interfaces do not have the bandwidth to handle the amounts of data that needs to be transmitted, so a new standard, available to the entire industry, that enables more sophisticated networking needs to be developed. As market demand for greater digitalisation grows, expect solutions like these to become a part of future trailer and truck builds.
- Enabling connected trailers for long vehicles – Trucks today are longer than they were in the past, and as the pressure on the logistics network grows, increased demand for greater efficiency may make them even longer. However, existing connection standards can only be used reliably with cables up to 15 metres long. For some applications, cables of up to 40 meters may be necessary, so hardware capable of handling these demands will be required. The hardware exists today, but it's manufactured in small quantities and carries a high price. As a result, trade organisations must work with chip manufacturers to ensure the truck industry doesn't get left behind as digitalisation advances.
- Ensuring safety – The weight, size and length of heavy goods vehicles makes the development of safe and effective driver aids very challenging. However, there is a demand for the kind of assistance measures that many motorists are used to, such as automated lane change or automated parking. Tools like these can reduce the load on truck drivers and increase efficiency – but they can't come at the cost of safety. As research and development continues, features like these will become more common, which could place new demands on body builders to integrate the needed sensors and cabling reliably.
Dealing with future disruptions
New technologies and a growing awareness of sustainability are creating new opportunities – but global-scale challenges will continue to affect business in the near future. Companies in our industry must adapt to meet them, whether through support from industry organisations or by increasing efficiency and lowering TCO through new equipment solutions. By reducing costs and minimising inefficiencies in areas you can control, such as production, service and support, you can at least minimise the negative impact of external factors.
